Table of Contents
1. Excess Inventory Definition
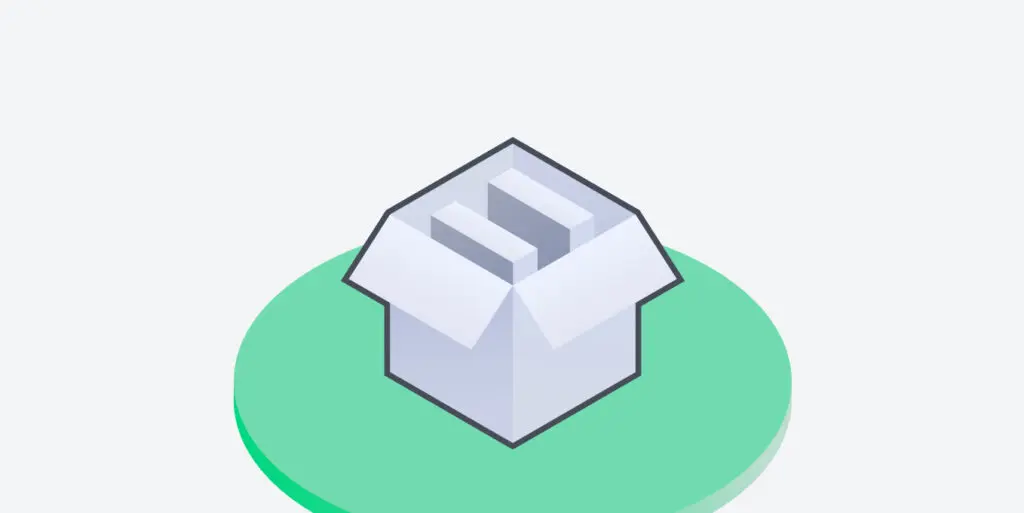
Products don’t always sell as quickly as anticipated by businesses. There are some items that stay on the shelves for too long because of consumers’ lack of interest in them. So eventually, these approach the end of their life cycle without getting sold. And that’s exactly what excess inventory is. Excess inventory refers to those products that companies keep for a very long time, failing to sell them in a timely manner. In the course of time, this inventory becomes an obsolete stock that carries no value.
When companies keep the inventory for too long, it starts losing its value and depreciates. So these good and materials lose the usefulness they once carried and companies have to get rid of it. So this “deadstock” gets written off companies’ books. There are numerous disadvantages of excess inventory that you want to avoid. So it’s essential that companies take steps toward reducing the amount of excess inventory they carry on hand.
There are companies that don’t give much attention to having extra stock. They believe that having extra stock is not necessarily a bad thing. Moreover, they think that they will manage to sell the inventory at some point for full price. Such an approach results in great losses for many businesses. Especially with perishable products, the excessive stock may exhaust the cash flow and result in loss of capital for inventing. So it’s crucial that companies always realize the importance of carrying an inventory of fresh products only.
In the rest of this post, we will present you with all the important knowledge regarding excess inventory. Why it happens, what are the disadvantages of excess inventory, how to sell it, and why to sell it? Pack yourself with ultimate knowledge regarding extra inventory.
2. What Causes Excess Stock?
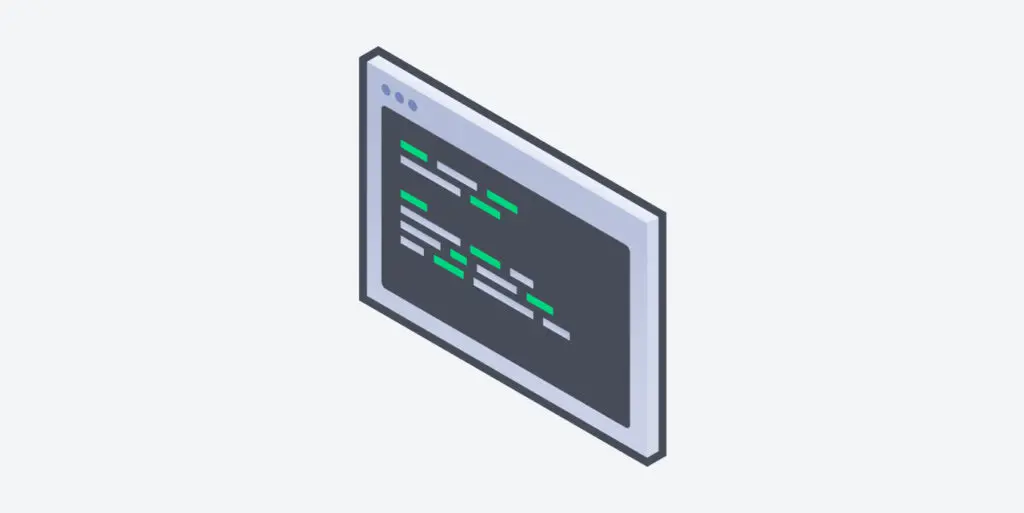
Inaccurate Demand Forecasting
We start with the basics: demand forecasting and planning. In today’s competitive world and fast-changing world, not having a demand forecasting system would be fatal for your company’s survival. Many business owners simply skip this step and find forecasts unnecessary to implement. However, they later find that bad forecasts or their lack are the leading cause of excess inventory. Using basic calculations of simple sales average or static ordering models won’t do the work.
When you conduct a forecast calculation, you need to take into account all the factors that can affect the demand. These include both internal and external factors. Internal factors are those that directly influence consumers’ desire to own the product. For example the seasonal trends. External factors are harder to predict because they affect buying habits indirectly. For example, consider whether changes or unexpected economic fluctuations.
You can forecast the demand either manually or use special software. If you run a bigger company, it’s best to rely on demand forecasting software because it will do the work more accurately and save you time.
Bad Inventory Management
Inventory must be well-managed in the company. Sometimes, you might end up having too much inventory because of a poor inventory management system. When the inventory management team lacks coordination and is unorganized, overbuying inventory is likely to happen. The inventory management team must be responsible for a number of tasks. For example, making transactions, ordering, purchasing, and all of the other tasks related to sales. When the management system is unorganized, this will result in poor inventory tracking and ordering mistakes.
The inventory management team must be also responsible for excess inventory management. Lack of organization inside the management team will lead to ignoring the slow-moving inventory and carelessness. So poor inventory management organization will result in inaccurate inventory tracking and ordering mistakes.
Supplier Constraints
Suppliers are a big part of your supply chain. Having a smooth and well-organized supply chain is essential for excess inventory management. If your suppliers are unreliable then you will face a lot of problems when making orders.
For example, consider the following scenario. You are making your orders timely, but your suppliers keep the products for an unknown period of time. Eventually, you get your order pretty late. You learn your lesson and put an order even earlier next time. In addition, you order way more than you need to cover the future demand too. So you put yourself into a riskful situation of ending with too much inventory. That’s why it’s essential to work with reliable suppliers who deliver your orders in a timely manner.
You want your suppliers to provide you with a realistic estimate of lead time. In fact, you don’t want anyone in your supply chain to add a safety factor to their lead time. When you know how long each member in your supply chain takes to accomplish their task, you will end up having a more efficient supply chain. And thereby, improve excess inventory management.
3. What Are the Downsides of Excess inventory?
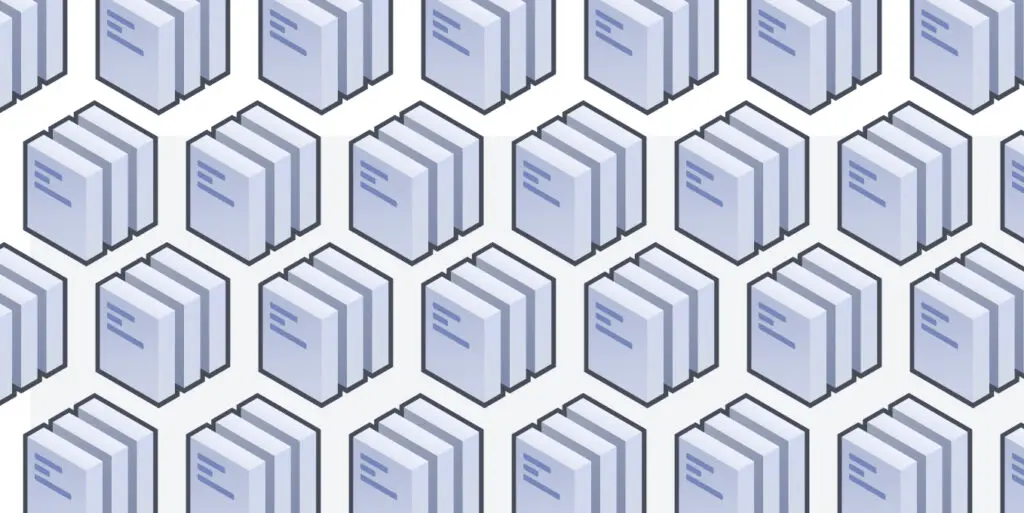
High Costs
One of the main disadvantages is that excess inventory may lead to big expenses. The cost of carrying inventory is high, and the cost of carrying excess inventory is even higher. When you have a lot of stock on hand, you need to store it somewhere. Usually, there are two options: you either rent a space or your store the inventory in your warehouse. Both of these options involve additional expenses.
If you rent a storage space, you will have to pay for it. If you have enough storage in your warehouse, you will still have to face extra expenses. Consider the utility costs for keeping the storage. You will also have to pay to employees who will be managing that inventory, which includes maintaining storage space, organizing the inventory, transporting it from one place to another, etc. And this is not the only drawback. If you decide to keep the stock in your warehouse, you will risk not having enough space for the new items.
Demand Variability
Consumer demand changes very fast. The inventory you have today can become obsolete tomorrow because of a drop in the demand. That’s why it’s essential that you order a quantity that corresponds to the amount you’ve initially forecasted. The worst thing that can happen to your inventory is that it can become useless. For example, consider food and medicine products. Keeping too much of such inventory on hand, you risk to throw them away as they deteriorate very fast.
When you order your inventory relying on a pure guess, you risk not to sell all the products. When you order too much inventory, eventually, the stock won’t sell because of demand variability. The more stock you keep, the higher’s the risk to lose it to demand variations. In fact, the best strategy is to always keep your inventory at optimal levels and not overstock it. The more inventory you keep, the more you risk of losing it to excess demand variations.
Negative Cash Flow
Last but not least, keeping too much inventory is a bad idea because it adversely affects your profit and cash flow. Since products depreciate over time, they eventually lose their initial value. The longer you keep a commodity product, the cheaper it gets. So excess inventory may lead to lower profit margin and loss of revenue.
Holding cost of extra inventory ties up cash that you could invest in other areas of your business growth. So first you spend money on buying the inventory, then you end up in ongoing expenses for holding that inventory. You also make sure to maintain it in a saleable condition. However, the inventory depreciates over time and you end up selling it for much cheaper than you’ve initially purchased it.
4. How Can You Identify Excess Inventory?
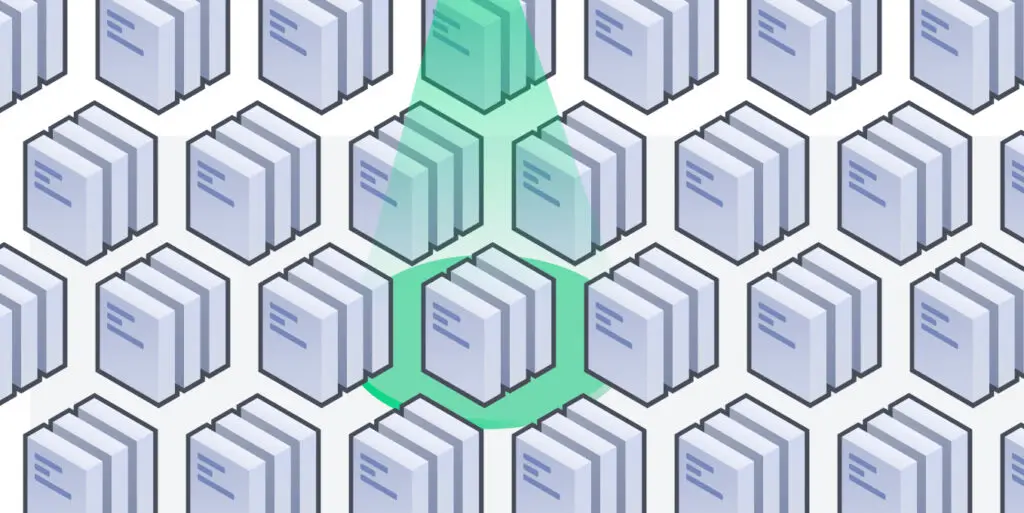
Sales per square foot = annual sales ÷ total square feet of storeThe higher is your SPSF the more efficiently your store creates sales based on your store’s space. This equation can be used for each department or section of your store. This is an especially useful tip for bigger stores because that way you will get more accurate results.
Days inventory outstanding = (average inventory ÷ cost of goods sold) x 365The lower your store’s DIO the better. This equation identifies how long it takes before the inventory turns into sales. For example, if your DIO is 40, this means that your store sells its entire inventory within a 40 day period. Keep in mind that the SPSF and DIO numbers vary depending on the industry. If you want to improve these metrics then compare yourself with the industry average. This way, you’ll understand how-well you store keeps up the sales and determine the extra stock you have.
5. How Can You Avoid Excess Stock?
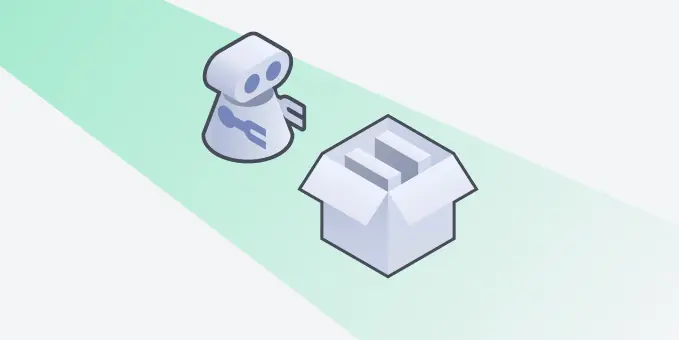
Excess inventory may lead to many problems, so it’s best to avoid it from the beginning. If you’ve already accumulated some extra inventory then you first need to determine how much of it you carry, as described in the previous section. After that, you can proceed to excess stock clearance. So once you’re done with that, the next step is to find the root cause and eliminate it. Below are the top 3 ways to avoid carrying too much stock and achieve inventory control.
1 – Planning Ahead
We’ve already discussed the importance of planning and forecasting. Failing to plan the inventory beforehand is the main root problem of having surplus inventory. To improve inventory management in your company you need to have end-to-end visibility in the supply chain processes. You also need to run real-time analysis of the inventory items.
Demand planning is also necessary for the successful implementation of the whole supply chain management. We’ve already stressed enough how important demand forecasting is. To plan the demand, you can either use demand planning software or do it manually. Both will provide you with a preplanned demand plan and schedule. Thus, you will avoid carrying too much inventory on hand, improve the supply chain visibility, and enhance customer satisfaction.
2 – Automating Processes
To achieve the maximum level of accuracy of internal operations, it is best to automate as much of the processes as possible. Manual operations can hitch the processes by slowing everything down. Today’s digital world provides companies with numerous solutions for dealing with such issues. You can adopt an inventory management software, demand planning and forecasting software, and finally, you can automate the ordering process.
Automating the ordering process will help ultimately avoid human errors. There are many benefits of the automated ordering process, including enhanced accuracy, efficiency, and speed of the automation. The visibility is improved within the supply chain processes, and tangible waste is eliminated because physical labor is not required. The automated process will resolve all the issues more quickly.
3 – Planning and Implementing Marketing Strategies
Although you can try to minimize the amount of excess inventory, it’s impossible to eliminate it entirely. The reason behind this is that it’s not possible to forecast the demand with 100% accuracy. And there will always be some inventory which won’t make it to sales. That’s why your business needs to have preplanned marketing strategies to implement, which will help you sell excess inventory. We will discuss the top strategies to sell excess inventory later in this post
6. What Is Inventory Turnover?
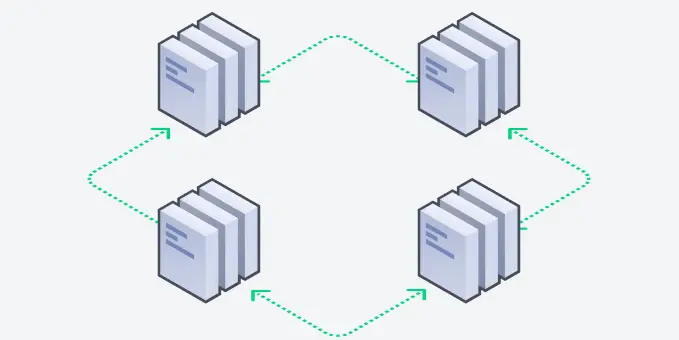
What is inventory turnover? Inventory turnover ratio is another helpful method for inventory control. It’s a metric that helps businesses identify how many times they sell and replace the entire inventory within a given time period. Simply put, it is an inventory to sales ratio. As the name suggests, the inventory turnover equation calculates how your inventory turns over and sells during a fixed period of time. The inventory turnover ratio is essential for business success.
The inventory turnover ratio formula has two important components: cost of goods sold (COGS) and average inventory. The COGS is usually found in the annual income statement. The average inventory is calculated by adding together the beginning and ending inventory and halving the number (divide by two). Once you have these two components, you can calculate the inventory turnover ratio. The inventory turnover equation is equal to COGS divided by average inventory. The COGS is also known as “cost of sales”, so the ratio is also referred to as inventory to sales ratio. The formula looks like this:
Inventory Turnover Ratio = Cost Of Goods Sold ÷ Average InventoryThe inventory turnover is a key measure of efficiency, as it calculated how much a business sell as a percentage of the total inventory it has. It’s a useful metric for the following reasons: It can be used as a comparison metric to industry averages and help identify your company’s performance in the market. It will give you insights and visibility into how well your company’s internal operations are coordinated, especially between sales and purchases. You will get an idea of how efficiently your company controls the merchandise It shows how liquid your company’s inventory is. Inventory is the biggest asset of the company. So it’s especially important for investors to see how well the company transforms inventory into cash. A low inventory turnover rate is an indicator that the company fails to turn the inventory into cash. So businesses should aim to achieve a high inventory turnover. However, the “high turnover ratio” is not a one-size-fits-all approach. Each company decides on its own what a “high rate” is. This depends on many different factors. You want to always compare your rate with the industry benchmark. This will give you a good understanding of where you stand. However, comparing yourself with only industry benchmark is not enough. You need to also take into consideration the size of your company. For example, you don’t want to compare your turnover rate with a company that’s in the same industry but is much larger. Small manufacturing operations don’t scale up to large manufacturing. So always take into consideration not only the industry but the size of the company too. And remember, a business should always strive to have a high turnover ratio for successful inventory control.
7. How Can You Sell the Excess Stock?
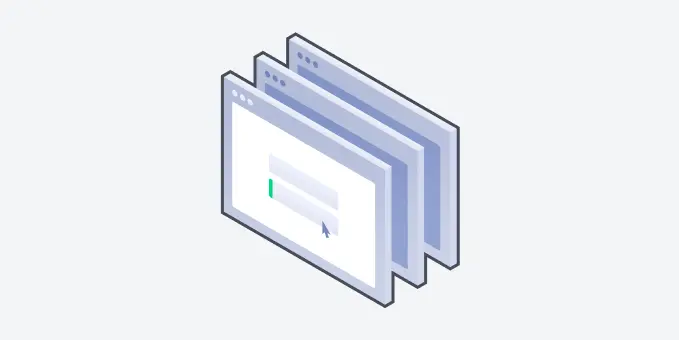
We’ve finally approached the most important question that bothers all business owners. How to sell excess inventory at a maximum? We present you the best techniques to get rid of excess stock, yet make some profit out of it.
1 – Liquidation
One of the most well-known ways of getting rid of surplus stock is liquidating excess inventory. Inventory liquidators buy all types of inventory and resell the products for a lower price. They specifically specialize in purchasing the excess stock that companies want to get rid of. So they are excess inventory buyers, who usually buy the products straight from the merchants.
Liquidating excess inventory is by far the fastest way to sell the inventory surplus you have. Yet, we have to say that it’s not the most profitable way. A liquidator usually buys the stock for a very low price. You also must consider the cost of delivering the inventory to the buyer. Be sure to work with a well-known and reliable liquidator, who won’t jeopardize your brand.
2 – Steep Discounts
Offering huge discounts is another great way to free your shelves from extra stock. Discounts work well for boosting the demand and sales for products. But it’s important to have a strategic approach when it comes to big sales. Discounts between 40-70% drive sales most efficiently. Consider running seasonal sales whenever the season is changing but you have some leftover inventory. This will help you avoid generating an excess old-season inventory.
Another sales type you can use is a flash sale. This one is one of the most effective sales because it creates a sense of urgency. Such sales are very attractive and they are available for a limited time only. So they have a strong psychological effect. Lastly, consider running clearance sales. These are often used specifically for excess stock clearance because the products are not selling well. It’s important to not run such discounts too often because people will get used to them. They will refuse to buy products at full price at the anticipation of sales.
3 – Bundling
Bundling is one of the most popular promotion techniques used by all retailers. It’s proven to be extremely effective. Bundling means pairing one product with another or even multiple products. A bundled offer is selling for a slightly lower price than if you sell the products separately. People often are very attracted to bundle offers.
When bundling your inventory items, follow the following rules. Bundle complementary products to create an attractive package deal. For example, consider bundling last season sunglasses that no one wants to buy with the latest swimsuits. Also, consider bundling fast-moving products with slow-moving ones. If a customer wants to buy a fast-selling product, there’s a big probability that they would pay a slightly higher price if that product is bundled up. Everyone loves a great deal with a discounted price!
Carrying excess stock has numerous disadvantages and is very costly. Unfortunately, it’s impossible not to have an inventory surplus at all. However, there are many ways to avoid it if you understand the main causing factors. And after all, you can use your company’s marketing efforts to create attractive offers to sell the leftover inventory. Always strive to make your inventory work for you and not against you. Keep your inventory turnover high and manage your stock for the long-term profitability of your business.
8. Are You Ready to Reduce Overstock for Your Business?
Reducing overstock involves solid planning strategies and smart tools, it can sound complex and demanding and for sure there are no magical tricks that deliver results.
The good news is that companies like Intuendi can share years of on-field expertise and AI-driven innovative tools to tackle the inventory optimization challenge.
Would you like to know what we can do for your company? Speak with our expert and get a free consultancy today.